Technology is changing healthcare fast, especially with 3D printing and prosthetics. 3D-printed prosthetics are not just new; they make rehab cheaper and more accessible. This mix is making affordable rehab a reality for many.
There are real-life examples showing how this tech works. It makes custom limbs quicker and cheaper. These advancements show tech can really help improve healthcare.
The Rise of 3D Printing in Healthcare
The healthcare world is changing fast, thanks to 3D printing. This technology is making medical devices better and faster. It’s changing how doctors and scientists make and test medical tools.
3D printing is making things cheaper and quicker. For example, prosthetics made this way cost $50 to $100. This is much less than the $1,500 to $8,000 for traditional ones. It’s a big help for people who need special prosthetics.
3D printing also makes devices faster. Some are ready in a day, while others take up to two weeks. This speed is key when patients need new devices quickly.
In 2008, the creation of the first fully 3D-printed prosthetic leg showed how powerful this tech is for affordable, custom solutions.
Companies like PSYONIC and Not Impossible Labs are leading this change. They’re making prosthetics like the Ability Hand and helping war refugees. These are great examples of 3D printing in healthcare.
NEWTEAM MEDICAL uses Raise3D Pro2 Series printers for medical prosthetics. They make things better and faster by not relying on others. For more info, read this article on medical 3D printing.
These changes are big for healthcare. 3D printing is bringing new ideas and making things more affordable. It’s a big step forward for healthcare.
How 3D-Printed Prosthetics are Revolutionizing Rehabilitation
The arrival of 3D-printed prosthetics has changed the medical world, especially in physical rehab. These new devices have started a big change, offering custom solutions that were once impossible.
One key benefit of 3D printing is making prosthetics more accessible worldwide. Old prosthetics were too expensive and took too long to make. But 3D printing makes them cheaper and faster, helping amputees get their prosthetics sooner.
This quick turnaround is a big help to patients. It means they don’t have to wait as long without their limbs.
- Ease of Customization: Personalized prosthetics fit each patient’s unique body, offering the best comfort and function.
- Speed of Production: What used to take months now takes days or hours.
- Cost Efficiency: Lower costs make prosthetics more affordable for more people.
Both patients and rehab experts love 3D-printed prosthetics. Dr. Jordan Smith from the Mayo Clinic says, “I’ve seen how 3D-printed prosthetics have changed lives for the better.”
“Before getting my 3D-printed limb, I struggled with daily activities. Now, I can move with ease and confidence,” shares Sarah, a recent amputee.
These stories show how important prosthetic access is for a real change in rehab.
The many 3D printing benefits, like better comfort and quicker delivery, show great promise. As we keep improving, we’re moving towards a future where everyone can get the prosthetics they need.
Cost-Effective Solutions for Amputees
3D printing has brought affordable prosthetics to amputees. This technology cuts down production costs a lot. It’s a big change from old ways of making prosthetics.
The economic impact of amputation is huge. Old prosthetics are very expensive. They cost a lot because they’re made the hard way. But, 3D printing makes good prosthetics cheaper. This means more people can get them.
Aspect | Traditional Prosthetics | 3D-Printed Prosthetics |
---|---|---|
Production Cost | $5,000 – $50,000 | $100 – $1,000 |
Production Time | Weeks to months | Hours to days |
Customization | Limited | Highly customizable |
The cost savings are big. It’s not just about making them cheaper. It also means less need for fixes and new ones. Plus, 3D-printed ones are lighter and easier to use. This makes life better for amputees.
In short, 3D printing in prosthetics is a game-changer. It makes prosthetics more affordable. This helps reduce the economic impact of amputation for everyone.
Bioengineering Prosthetic Technology
Bioengineering has changed prosthetic technology a lot. It uses new research to make 3D-printed prosthetics better. Bioengineers work together to find new ways to make prosthetics work better.
New synthetic materials are key to these changes. They feel like real limbs. This makes prosthetics more comfortable and durable. They also don’t cause as much irritation, so they’re easier to wear for a long time.
Prosthetic integration has also improved a lot. Thanks to nano-engineering and smart materials, prosthetics can change with the body. They respond like muscles and tissues, making them work more like real limbs.
Bioengineering advances show how teamwork is changing prosthetics. Engineers, doctors, and material scientists are working together. This has led to prosthetics that are more custom and functional.
These efforts mean prosthetics will soon be even better. They will not only work well but also make life better for amputees. The ongoing work on materials and integration is making prosthetics more adaptable and user-friendly.
Customizable Prosthetic Solutions
3D printing has changed prosthetics a lot. Now, prosthetics can be made just for you. This means better fits and more function for everyone.
Sarah Reinertsen is a great example. She lost her leg young but thanks to 3D printing, she races and stays active. Her story shows how prosthetics can change lives.
These prosthetics are made fast now. What took weeks or months before, can be done in days. This means people can get back to their lives sooner.
Here are some big benefits of these prosthetics:
- They fit better and are more comfortable
- They work just how you need them to
- They’re made faster and cheaper
With 3D printing getting better, prosthetics will keep getting better. This means a better life for many people.
Applications of Additive Manufacturing for Prosthetics
Additive manufacturing, also known as 3D printing, has changed prosthetics forever. It makes every step from design to product better. It’s all about saving money, making things fast, and customizing them perfectly.
One big plus of 3D printing is how fast it works. It can turn digital designs into real prosthetics quickly. This is great for medical needs, where time is everything.
Now, we can make prosthetics that fit each person perfectly. This used to take a lot of time and money. But 3D printing makes it easy and affordable, ensuring prosthetics fit well and work great.
The National Institute of Health has mentioned, “Additive manufacturing allows for the creation of lighter, more durable prostheses that can be produced at a fraction of the cost compared to traditional methods.”

Also, 3D printing lets us add smart materials and sensors to prosthetics. This makes prosthetic limbs work better and feel more natural.
The benefits of additive manufacturing are clear in many areas:
Aspect | Additive Manufacturing Benefits |
---|---|
Cost | Significantly Reduced |
Customization | Highly Personalized |
Production Speed | Rapid Prototyping |
Material Versatility | Wide Range of Choices |
Functionality | Enhanced with Smart Materials |
In short, additive manufacturing has opened up new possibilities for prosthetics. As 3D printing gets better, we can expect even more advanced and helpful prosthetics in the future.
Patient-Specific Prosthetic Devices
Thanks to 3D printing, making prosthetics just for you is now possible. Precise 3D scanning makes sure they fit perfectly and work great for each person.
The first step is using precise 3D scanning and modeling. This captures the exact shape and size of your limb. This way, the prosthetic is made just for you, fitting your body perfectly.
These prosthetics are made right in hospitals using patient-focused technology. Doctors and patients give feedback to make them even better.
Here’s how 3D-printed prosthetics compare to old ones:
Aspect | Traditional Prosthetics | 3D-Printed Prosthetics |
---|---|---|
Customization | Limited | High |
Production Time | Weeks to Months | Days to Weeks |
Cost | High | More Affordable |
Fit and Comfort | Standard | Personalized |
Individualized prosthetic design is used in many areas like orthopaedics and oncology. With patient-focused technology and 3D scanning, doctors can help patients recover faster. This makes the whole healing process better and more effective.
Prosthetic Design Optimization
Prosthetics are changing fast, thanks to new design ideas. Now, prosthetic limbs are more functional and comfortable. This is all thanks to 3D software, which lets designers make prosthetics that fit each person perfectly.
With 3D software, making prosthetics is faster and more precise. Designers can try out new ideas quickly and make changes fast. This means prosthetics keep getting better over time, thanks to feedback from users.
Making prosthetics comfortable is key. Designers focus on making them fit well and feel right. This makes prosthetics a big help in daily life for those who use them.
In short, new 3D software and ergonomic designs are making prosthetics better. This is a never-ending journey, driven by new tech and user feedback.
Transformations in Prosthetic Limb Manufacturing
3D printing has changed prosthetic limb making forever. Modern methods have made prosthetics better and faster. Digital tools let makers design limbs with great detail and personal touch.
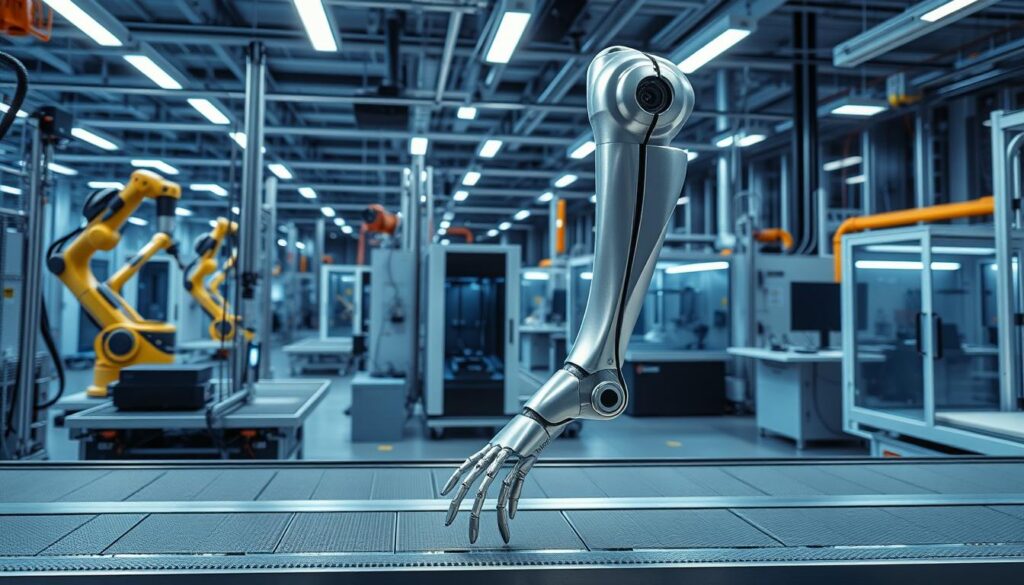
Now, making prosthetics can be done on a big or small scale. This means making one custom limb or many parts quickly. Companies like Össur and Hanger Clinic use these new ways to help patients more.
More people want 3D-printed prosthetics because they’re flexible and affordable. As new tech comes in, making prosthetics will get even better. We’ll see more use of IoT and AI, making limbs even more precise and efficient.
Advanced Prosthetic Fabrication Techniques
New methods in prosthetics have led to better and more realistic prosthetic limbs. Breakthroughs in materials and 3D printing have changed the game. These advancements have set new standards in the field.
Lightweight, strong materials like carbon fiber and advanced polymers are key. They make prosthetics last longer and work better. They also allow for detailed designs and custom options.
At places like the Massachusetts Institute of Technology (MIT), experts are making prosthetics better. They’re working on making prosthetics move more naturally. This improves life for people who have lost limbs.
Adding sensory feedback systems is another big step forward. These systems include sensors that mimic touch and balance. This makes prosthetics more intuitive and useful in everyday life.
These advancements show the power of teamwork between engineers, doctors, and researchers. The future of prosthetics looks bright. Ongoing innovations will make prosthetics even better and more accessible.
Innovations in the Prosthetic Industry
The prosthetic industry has seen big changes lately. Thanks to new designs and technology, prosthetics are now more advanced. Companies like Össur and Ottobock have led these changes.
Now, prosthetics can be controlled by brain signals. This means users can move their prosthetics more naturally. It makes everyday tasks easier and more intuitive.
Advanced Arm Dynamics and Coapt are also making big strides. They’re improving prosthetics so they can grip better and feel like real limbs. These advancements are setting new standards in the industry.
Here’s a look at some key advancements in prosthetics:
Year | Technology | Company |
---|---|---|
2015 | Myoelectric Hands | Touch Bionics |
2018 | Neurological Signal-controlled Limbs | Össur |
2021 | Feedback Systems for Touch | Coapt |
2023 | Fully Integrated Bionic Arms | Advanced Arm Dynamics |
3D Printed Prosthetics: Coverage and Impact
3D printed prosthetics have seen a big rise in recent years. This is thanks to lots of media coverage. They are now more affordable and can be made to fit each person’s needs.
Media like The New York Times and National Geographic have shared stories about these prosthetics. They show how this technology is changing the industry. This coverage has helped spread the word and push innovation forward.
3D printed prosthetics do more than help people move better. They also help people feel more included in society. They give people the chance to be more active and confident in their communities.
Studies show that these prosthetics are also saving money. This means more people can get them. Their growing use is changing how we think about helping people recover from injuries.
Aspect | Traditional Prosthetics | 3D Printed Prosthetics |
---|---|---|
Cost | High | Reduced |
Customization | Limited | High |
Production Time | Weeks to Months | Days to Weeks |
Accessibility | Restricted | Broadening |
As technology keeps improving, the impact of prosthetics will grow. Media will keep playing a big role in sharing this news. The benefits of being more accessible and included are huge. This all points to a bright future for 3D printed prosthetics.
Conclusion
The future of prosthetic technology is changing fast, thanks to 3D printing. This new method makes prosthetics cheaper, more custom, and better for each person. It’s making a big difference in how we help people recover.
3D printing is making prosthetics better in many ways. It helps make them more precise and affordable. This means amputees get prosthetics that really fit their needs. And, the field is always getting better, offering even more hope for the future.
Experts like those at MIT’s Media Lab and Open Bionics see big changes coming. They say 3D printing could change lives. But, we need to solve problems like getting these prosthetics to more people. Still, the future looks bright, full of hope and new chances for everyone.